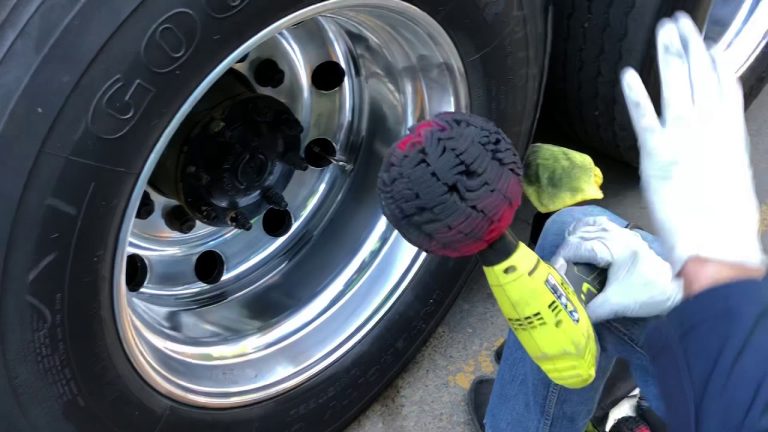
When you want to improve the appearance of your aluminum products, a professional metal polishing service is your best bet. A polished surface not only gives your products a more professional look, but also enhances chemical resistance and makes them easy to clean.
The metal polishing process uses abrasion compounds to remove surface imperfections and creates a uniform grain preparing the part for inspection and other finishing processes.
Finishing
Aluminum Polishing Services is a remarkable material that offers many benefits and properties. Its innate ability to form a glass-hard, transparent oxide film on its surface protects it from environmental stress such as corrosion.
However, this protection alone isn’t enough for some applications. In these cases, additional protection is needed to preserve the integrity and appearance of the product.
Finishing methods include mechanical, chemical, and organic coatings. They are used to enhance the appearance or performance of an aluminum extrusion or trim.
Commonly used in storefronts and trim, wall corner guards, exterior panels, infill railings, handrail posts and more, these processes alter or remove the existing layer of the metal to create a new surface. They can also improve the physical properties of the metal or clean it to remove burrs, radius edges, etc. These processes can be performed using standard or custom equipment, depending on the specific requirements of each application.
Surface Preparation
Aluminum is a versatile metal that’s used in a variety of applications. It’s a light and strong metal that is also resistant to corrosion, making it a great choice for a wide range of industrial applications.
However, over time, aluminum surfaces can become dull and discolored. A good way to revive an old aluminum surface is by polishing it.
The process of polishing requires a variety of abrasive tools. The most common tool used in this process is an angle grinder with a buffing wheel.
Another effective tool for surface preparation is a bristle blaster. This tool can remove stubborn dirt from a surface, such as rust or mill scale. It also allows a new coating to be applied to the surface without the risk of adhesion problems.
Deburring
Burrs are small ridges that often appear on machined metal parts. They can make them unattractive and affect the quality of finished parts.
Deburring is an important finishing process for metal parts. It helps to eliminate all imperfections on the surface after welding or machining, leaving behind smooth, quality metal parts.
There are many different deburring methods available, ranging from manual to electrochemical. However, most manufacturers choose an automated method when possible to save time and effort.
Mechanical deburring is a very versatile and low-cost method for eliminating burrs. It is particularly suitable for removing burrs that are too large for other deburring techniques to handle.
Depending on the material, the shape of the burrs, and the severity of them, different mechanical deburring procedures are used. This method can be performed on various shapes and sizes of parts, including turbine blades and other tools.
Electropolishing
Electropolishing is a highly effective finishing process that smoothes the microscopic surface of most metals. The treatment also removes heat tint, oxide scales and improves corrosion resistance.
In the electropolishing process, a workpiece is hooked up to a power supply and placed in a temperature-controlled chemical bath, typically containing a high-viscosity mixture of sulfuric and phosphoric acid. An electric current is then applied to the part.
The combination of the chemical bath and electrical current allows the dissolution of micron-level surface layers, smoothing out burrs and sharp edges to reveal a shiny, polished part. The smooth surface also prevents the part from collecting contaminates.
Electropolishing can also be used to eliminate large pores that are sometimes present in cast parts. If a part has a large number of pores that are filled with dirt and glue, the result will be a dull finish. This condition is commonly referred to as a “zebra stripe.”